Automatic Train Control: Efficient Validation of Safety-Critical Functionality
Validating Automatic Train Control (ATC) systems requires iterative testing cycles throughout the product’s life. Safety, reliability, and functionality must be rigorously tested each time the system is updated to ensure optimal operation for modern signaling applications like CBTC and ETCS. PSA’s expertise in validating safety-critical rail hardware and software underpins robust and reliable validation processes, ensuring that the entire system operates as designed.
Automatic Train Control: Key System Testing Components
ATC systems encompass several critical functionalities:
-
Automatic Train Protection (ATP) – cab systems responsible for proper acceleration, braking, stop, and speed profiling based on Limits of Movement Authority
-
Automatic Train Operation (ATO) – onboard and wayside systems that enable coordinated driver assistance or unmanned train operation
-
Automatic Train Supervision (ATS) – centralized dispatching systems aimed at coordination of train movement and schedule adjustment
Regardless of how many of the above components the train control system includes, they must be rigorously tested each time changes are introduced to the original. That is, when installed along the track, on the locomotive, or any component undergoing modifications while operating, it’s crucial to test the smooth operation to validate the module upgrades do not affect the behavior of the entire system. PSA leverages solid and proven frameworks to ensure critical system modules operates without a hitch, implementing White Box and Black Box testing for wayside, carborne, and communication hardware, utilizing best-in-class testing tools and simulators.
System Validation of Automatic Train Control: Common Pitfalls
Organizations that use Automatic Train Control Systems (ATCS) face validation challenges that affect system safety and reliability. A team's understanding of these common issues helps create reliable validation strategies. Let’s figure them out.
Inadequate requirements analysis
Requirements analysis is the life-blood of successful ATCS validation. Organizations struggle with incomplete or poorly defined requirements that create validation gaps. A detailed requirements analysis must account for both functional and non-functional aspects of the system. These challenges persist:
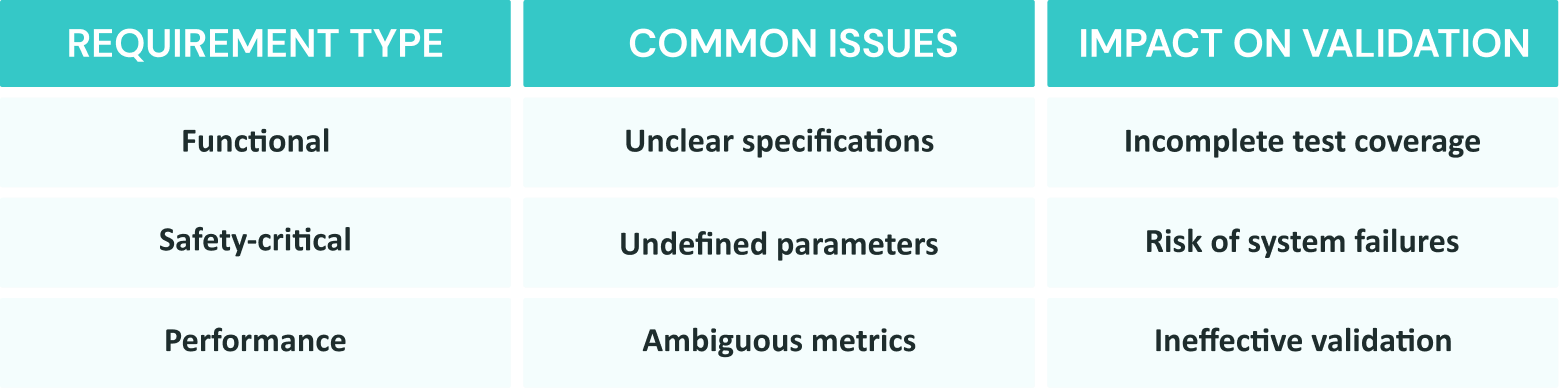
Test coverage gaps
Test coverage gaps pose the most important risk in Automatic Train Control system validation. Organizations that target specific coverage percentages (typically 80-90%) often create a false sense of security by focusing on metrics alone. Critical considerations include:
-
Teams skip edge cases and boundary conditions
-
Safety-critical functions remain partially tested
-
Subsystems lack proper integration testing
-
System failure modes and recovery scenarios need more testing coverage
Poor documentation practices
Organizations face documentation challenges because of inconsistent practices and lack of standardization. It commonly include missing connections between requirements and test cases, test procedures and results lack needed details, weak version control, and incomplete change records management. Effective documentation needs to support current validation work and future system changes. This ensures detailed tracking of validation processes and their results.
Lack of domain expertise
Validation teams must understand both railway operations and principles of Automatic Train Control. When this domain expertise is lacking, critical scenarios are often overlooked, particularly in safety-critical software validation. Engaging field experts can improve validation planning and coverage. Field workers' hands-on knowledge of system operation and maintenance helps teams create better validation plans. Integration of domain expertise in the validation lifecycle gives complete coverage of operational scenarios and possible failure modes.
Efficient Testing Frameworks for Products Validation of Automatic Train Control
ATC Validation Scope
A well-laid-out validation plan needs a structured approach that includes all system components and interfaces. A good validation plan has these elements:
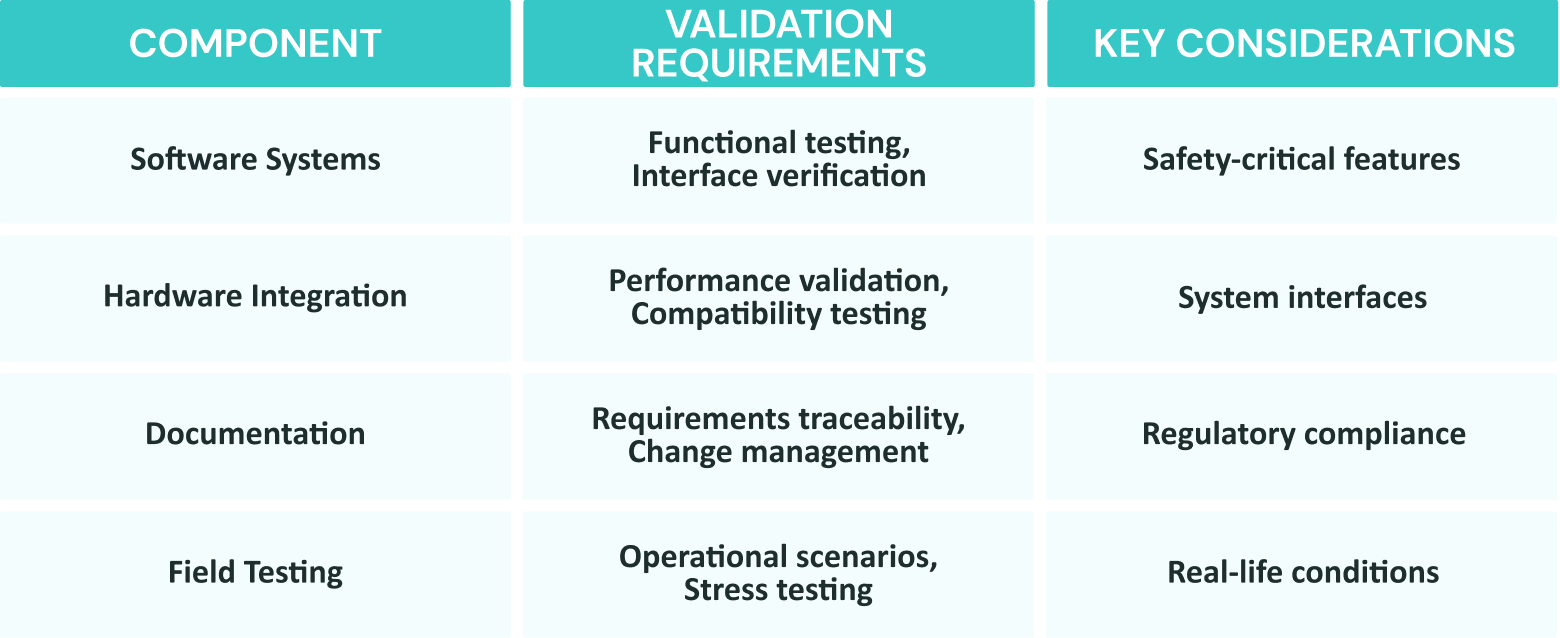
At PSA, we conduct independent validation by setting clear objectives, timelines, and success criteria for each phase. We use both static and dynamic testing methods to effectively track and manage changes throughout the process.
Requirements Validation for Automatic Train Control
ATC systems are essential to modern railway operations, automating various functions to enhance efficiency and safety. Since rail systems typically operate for 15+ years, verified documentation is also crucial for future system upgrades and certification. Comprehensive and validated documentation helps maintain high-quality standards in the design, development, and deployment of Automatic Train Control systems, supporting key processes such as traceability and compliance verification.
A train control system requires a thorough understanding of critical safety requirements to ensure reliability. Engineering these requirements before or after the modules are designed can be challenging, but necessary to document purposes, constraints, and functional requirements for each system module. Effective requirements engineering should clearly define both vital and non-vital system functions, supporting basic and advanced applications, including various types of interlockings, interfaces to field devices, warm and hot-standby configurations, train detection, and CBTC support.
Leveraging VectorCAST for ATC Software Validation
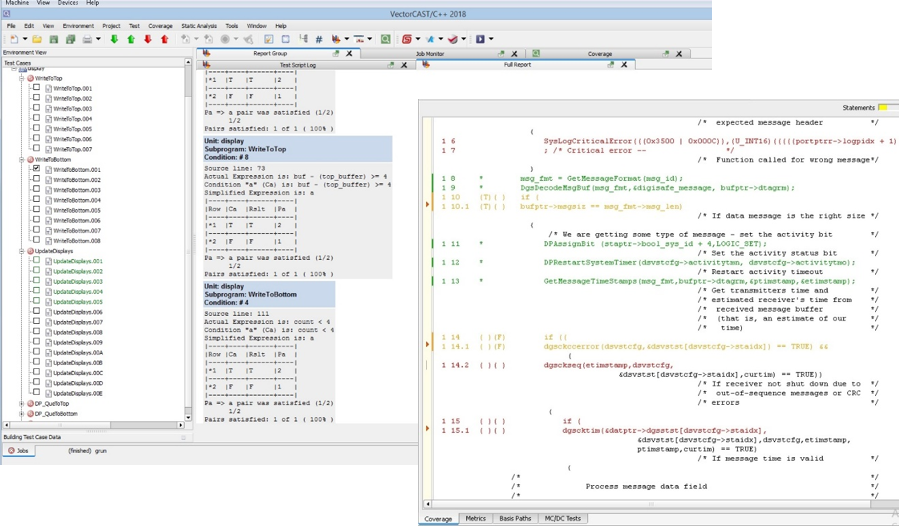
When validating safety-critical rail software, VectorCAST is a powerful tool that supports automated testing of ATP, interlocking, train control, and signaling systems. VectorCAST provides automated dynamic testing and code coverage analysis, critical for SIL4 verification and ensuring compliance with standards such as:
-
EN 50128: Software requirements for railway control and protection systems
-
IEC 62279: Communication, signaling, and processing systems
PSA’s expertise with VectorCAST enables efficient verification of software updates, new module integrations, and RAMS (Reliability, Availability, Maintainability, Safety) validation. We ensure comprehensive safety validation within accelerated timelines by leveraging the following key features of the tool:
- Automated unit and integration testing enabling continuous workflows
- Static code & code coverage analysis
- Requirements traceability, crucial for regulatory compliance environments. Continuous integration can be carried
- Test management and detailed reporting
Board-Level Tests with LabVIEW
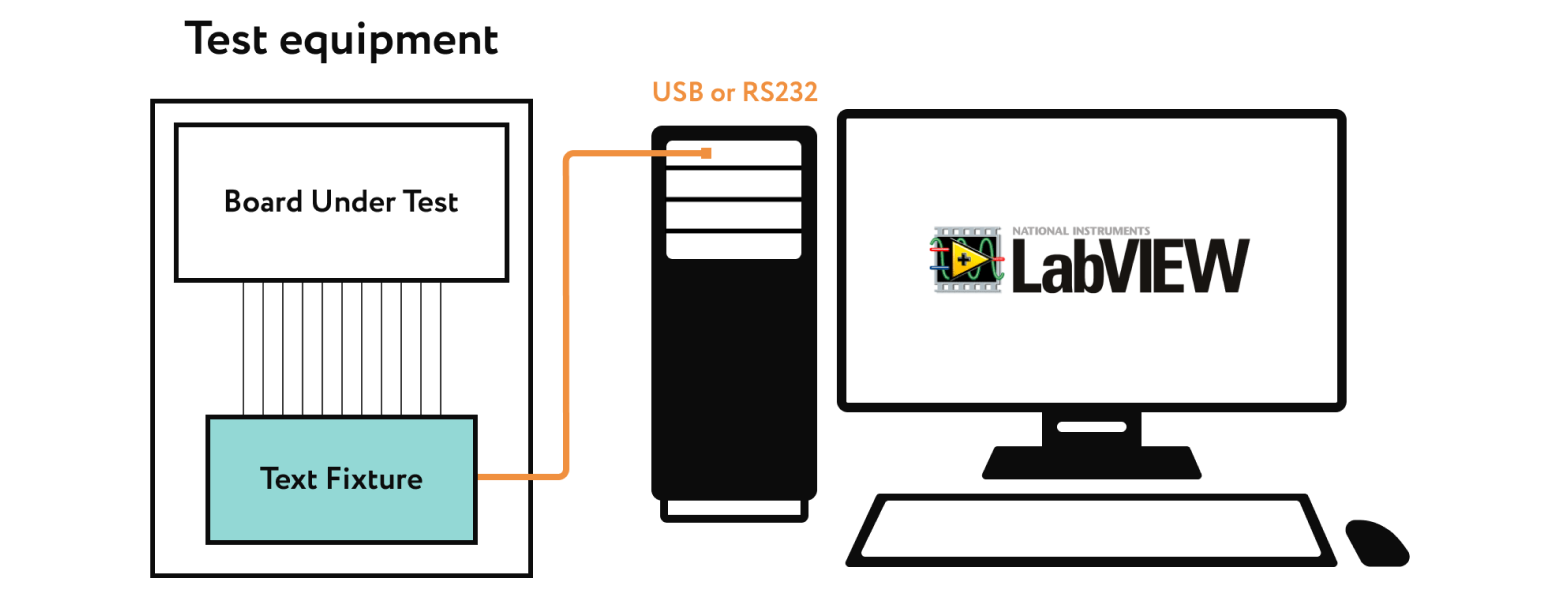
LabVIEW is a powerful tool that offers a graphical, model-based approach to testing and programming vital boards. It seamlessly integrates with a wide range of hardware to simulate real-world conditions and capture accurate data during validation tests. This allows for the simulation of multiple rail scenarios, ensuring the proper operation of interlocking, train, and dispatching systems. PSA skilfully utilizes LabVIEW to simulate and validate system behavior across various scenarios, including fault conditions, to ensure robustness and reliability.
LabVIEW’s intuitive graphical interface simplifies the design and organization of test sequences, allowing us to easily replicate real-world conditions through simulations and models. Additionally, we help our clients optimize and enhance LabVIEW testing by upgrading the outdated test models and engineering custom testing fixtures to support the validation of highly specialized or legacy rail equipment.
Looking for a Reliable Validation Partner?
Simulation and Virtual Commissioning for Automatic Train Control
Virtual commissioning marks a transformation in ATCS validation that lets you test systems thoroughly in a risk-free environment. PSA can validate control logic, hardware integration and system response by creating virtual environments. Native communication with PLCs happens directly in the virtual commissioning environment, where we manage high-speed I/O traffic carefully. Advanced simulation tools support various testing scenarios such as:
-
Manufacturing simulation to validate ladder logic
-
Multi-PLC testing environments
-
Network communication verification
-
Emergency response validation
PSA's virtual commissioning approach has shown significant cost savings while speeding up system implementation. Teams can now schedule aggressively during shutdown periods and make detailed changes within tight timeframes.
Advanced tools and techniques help PSA's steadfast dedication to validate documentation thoroughly, prepare datasheets precisely, and participate in expert commissioning. These technologies make validation processes more efficient while upholding strict safety standards for Automatic Train Control Systems.
Customization Needs for Testing Frameworks of Automatic Train Control
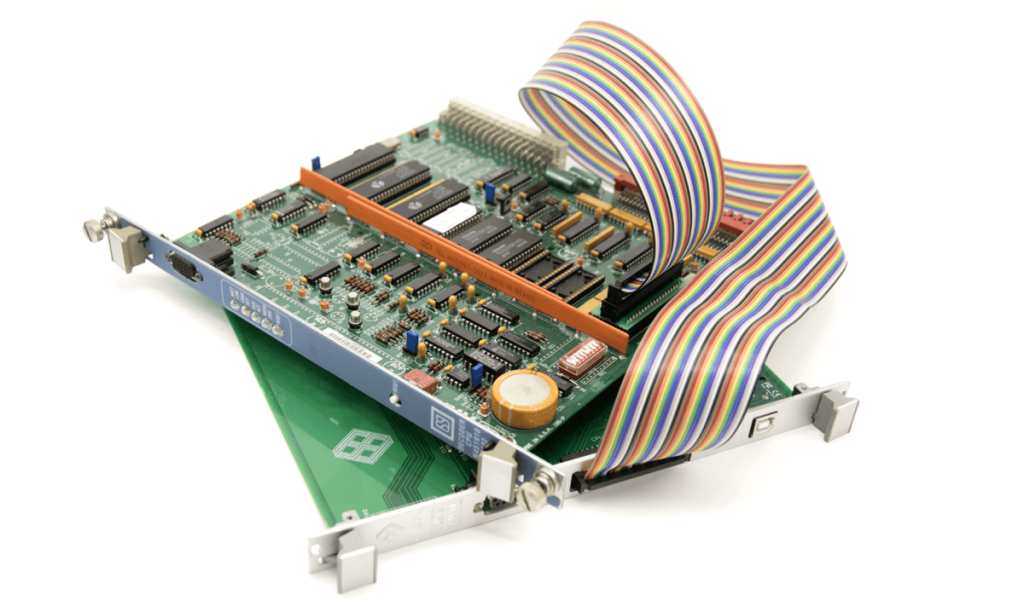
PSA-engineered custom fixture for LabVIEW testing
With an average lifespan of 15 to 30 years, train control system components eventually become obsolete, requiring custom solutions not only to maintain signaling efficiency but also for testing. Introducing custom test fixtures for onboard or wayside equipment is standard practice; however, it demands deep and specialized expertise. PSA test engineers are skilled in both legacy systems and modern technologies to ensure thorough comprehensive validation.
Custom testing tools are often necessary for proprietary systems. The PSA team develops these tools, dives into your custom tools and optimizes them, enabling faster, more cost-effective testing of critical infrastructure.
Summing Up
-
Automatic Train Control systems need rigorous, ongoing testing to ensure safety, reliability, and performance, especially after updates, for applications like CBTC and ETCS.
-
Key ATC functions—Automatic Train Protection (ATP), Automatic Train Operation (ATO), and Automatic Train Supervision (ATS)—undergo thorough testing to prevent disruptions across the system.
-
Effective ATC validation tackles common issues like gaps in requirements, test coverage, and documentation, as well as domain expertise, ensuring accuracy and reliability..
-
With 15+ years of expertise, PSA leverages VectorCAST for automated testing, LabVIEW for board-level validation, and virtual commissioning to simulate real-world conditions, enhancing efficiency and regulatory compliance.
-
Given ATC components’ 15–30-year lifespan, PSA provides custom test rigs and updates legacy equipment to sustain signaling efficiency and validate critical infrastructure.