Beyond Traditional Warehouse. How IoT Makes Warehouse Automation More Affordable
Even if a vehicle suddenly breaks down at the halfway point or subcontractors delay cargo without reason, warehouse operations can and should be a safe harbor for supply chain management. The rapid evolution of enterprise IoT solutions has made this potential a reality, not just for big corporations heavily invested in end-to-end automation, but also for small and medium sized enterprises (SMEs) with smaller warehousing facilities to address operational challenges through warehouse automation.
Advanced robotization is not justified for every warehouse. Not everyone is okay with maintaining a certain warehouse configuration under bulky equipment or implementing multiple related solutions for the correct operation of top-notch technologies. IoT sensors, processing nodes, and cloud storage are the only components to succeed with warehouse automation for both particular processes and the whole warehouse involving all the measurable resources in a smart network. Thus, by mastering IoT, any industry player can make a warehouse the most durable and predictable logistics link.
Warehouse Automation: How IoT Pushes the Boundaries of Its Traditional Nature
It is common and quite effective to rely on GTP systems to automate packing, retrieving, and other physical processes, while WMS facilitates operations management. Many industry players opt for adjustment of their space and investment to them, while IoT is much easier to adjust to existing environmental and business conditions. By understanding how to handle a flexible IoT fabric, you gain:
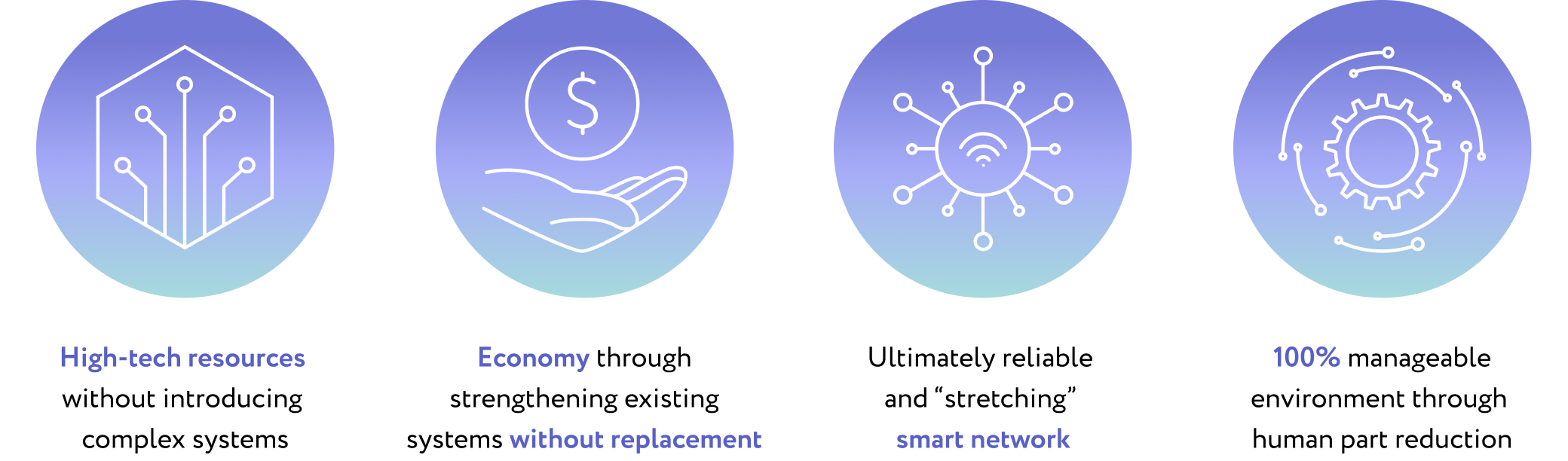
Thus, IoT is best for initial warehouse automation to connect the physical and digital worlds. Also, IoT solutions can become the basis for end-to-end warehouse automation and develop into a complex network as the business scales. After all, they can be applied to advance already automated warehouses bringing new features and creating a more connected environment.
Warehouse Automation: Storage-Retrieval Processes
IoT assists in placing and retrieving goods from a warehouse by providing the most precise data on location, quantity, quality, parameters, and so on. The exact location of goods can be guaranteed by an RFID long-range identification system. Connection to the enterprise network or an AS/RS control system guarantees data-driven management with the highest accuracy, eliminating manual identification, tag damage, and loss of objects while reducing efforts tenfold. The role of RFID tags for various cases can also be performed by presence or infrared sensors, as well as machine vision systems. You can mark various categories of goods that require special storage and transportation conditions, such as fragility, to provide safety throughout the supply chain.
Next, IoT provides better control of worker safety when interacting with AS/RS. Namely, detecting the presence of a worker and analysis of their behavior with real-time monitoring of the system’s position and activity allows for prompt notifications of possible dangers. By collecting information from AS/RS equipment sensors, you can also run it through in-depth analysis to predict upcoming failures and prevent hazards, respectively.
Warehouse Automation for Inventory Tracking
A simple targeted IoT application allows you to bring inventory accuracy as close as possible to 100%, eliminating asset theft, damage, miscalculations, and even predicting shortages from suppliers. How to get a warehouse at a glance?
Firstly, IoT provides advanced and easily scalable security solutions to eliminate any kind of breaches. Presence, thermal, PIR, or other relevant sensors can be located pointwise to secure required locations. It becomes much more transparent to manage access in connected environments by introducing NFC cards, biometrics authentication, or machine vision recognition. In connected environments, various data flows to the analysis module to identify small breach indicators. For instance, complicated AI-based systems can be adjusted to analyze worker’s behavior and look for deviations.
Secondly, permanent IoT-based tracking ensures compliance with storage conditions and minimizes the likelihood of damage. This includes both simple environmental monitoring such as temperature or humidity and more specific monitoring such as chemical, particle, or interstitial, which can be required for potentially dangerous assets. Thus, IoT helps meet warehouse automation safety standards
Thirdly, IoT-based tracking excludes human error when checks and calculations while cloud connectivity provides 24/7 access to inventory data from any place.
Warehouse Automation: Equipment Maintenance
By implementing IoT-based maintenance, you can eliminate delays in the warehouse caused by equipment downtime. By knowing about an impending breakdown in advance, you can assign necessary maintenance in advance as well as get rid of unnecessary regular service. Technologically, you equip your machinery with sensors to keep key components of your machines and vehicles under constant control and receive immediate alarms with the first signs of upcoming issues. Vibration, sound, and thermal sensors are commonly used for machine monitoring, but any solution can be tailored to a specific request.
Typically, the warehouse equipment fleet is not exacerbated and does not require unique items, which makes Condition-Based Maintenance (CBM) suitable for it. With this method, the smallest hints of upcoming failures are detected and signaled upon the occurrence, in contrast to Predictive Maintenance (PdM) which involves complex machine learning algorithms to detect the problem much ahead.
Need Help?
Warehouse Automation: Intensive Collaborative Environment
The most advanced warehouse tools utilize IoT robotics or cobotics, improving the interaction between humans and machines.
Collaborative robots (cobots) in warehouse automation can be responsible for labor-intensive mechanical duties such as screwing, assisting in sharpening knives, assembly assistance and inspection, folding and packing, picking and sorting, and so on. Cobots can assist with the allocation of arrived goods, checking quantity and specific parameters, and control storing asset parameters, such as wear and tear of pallets. With cobots equipped with machine vision, we can expect increased operation accuracy and enhanced safety of operations, since cobot sensors can track the motion and approximation to avoid human-cobot collisions.
Warehouse Automation: Advanced Analytics for Operational Optimization
We have mountains of valuable IoT data, millions and billions of records that can and should be helpful. Having a super-sampling, we launch advanced analysis and gain improved forecasts to improve strategies of warehouse operation.
IoT-based analytics allow us to find out the tiniest patterns in equipment, staff, and even 3-party behavior thanks to redundant information and machine learning algorithms. Sensors and RFID tags allow for tracking of the exact location in real-time and with complete information about the product. Having a complete view of your warehouse processes, you can tweak them in a knowingly correct way. For example, you can track repeat order sets to optimize storage space and minimize order picking time. Also, you can send the picker along the optimal route, from heavy to light goods to be collected. You may suddenly find some of your suppliers usually delay through the bad weather and adjust your operations to this fact or put thought into determinations of a contract.
Augmentation of WMS – IoT-Based Warehouse Automation
The IoT application can be used as a separate management tool for a specific warehouse process, as well as an extension connected to the existing Warehouse Management System (WMS). It boosts the WMS-delivered efficiency through the IoT data collection is of the highest quality. Thanks to comprehensive tracking, and increased visibility in real-time, the receiving and placement, order picking, packing, and fulfillment, shipping, inventory control, labor management, yard and dock management, and other related processes can be substantially improved automatically.
Warehouse Automation Based on IoT – Crucial Features to Get along with
When creating IoT-enabled products and solutions for warehouse automation, meeting specific warehouse conditions with IoT capabilities is critical.
-
24/7 Real-Time Operability. IoT devices for warehouse automation should be real-time systems. With the process autonomy increased, delays in such systems have to be minimized.
-
Top-notch Security. Develop strict IoT cybersecurity policy in advance. First, most IoT devices are insecure by default. Second, when relying on 3-party systems, you also devote cyber security measures to this 3-party.
-
Interoperability. Consider the need to collect data from both digital and analog assets for legacy, as well as real-world objects.
-
Physical Receilince. IoT devices should be adequately protected against damage. For example, utilizing anti-vibrational frames when PCB design ensures complete data collection even after an accident.
-
Scalability. IoT products have to freely connect to the cloud to ensure scalability with minimal resource costs. This is especially critical for small and medium-sized warehouses.
Thus, IoT for warehouse automation is more than sensor-based data collection – it’s an integral ecosystem, which streamlines all the warehouse processes. Want to know how to provide elegant operations without over-complexing the warehouse? Collaborate with PSA for the balanced IoT logistics solutions.