In highly connected environments like IoT ecosystems, any node can potentially provide access to critical infrastructure, central operations, or data storage. Robust encryption, network segmentation, and advanced access controls are essential. Additionally, new practices and customized security solutions should be tailored to the specific needs of each production environment.
IoT in Manufacturing: Smart Approaches for Targeted Troubleshooting
But what if machines could tell us when they're about to fail? IoT in manufacturing is indispensable for achieving this goal. The innovative techs behind IoT are revolutionizing troubleshooting and maintenance processes, enabling manufacturers to catch minor problems before they grow into costly challenges, thus keeping production lines humming.
By involving IoT in manufacturing operations, companies not only gain a technological upgrade but also achieve unmatched flexibility in strategy planning, enhancing their competitiveness in complex industrial environments. This article provides a comprehensive overview of IoT-enabled applications to empower troubleshooting and maintenance in manufacturing. Get ready to discover how IoT is shaking up the factory floor promoting efficient and cohesive operations, as well as smart, well-informed decision-making.
IoT in Manufacturing: Revolutionizing Maintenance & Troubleshooting
When it comes to IoT in manufacturing, troubleshooting is intended to identify and resolve system or process issues quickly. Typically, it involves addressing equipment malfunctions that cause downtime, safety hazards, and quality issues. IoT has become a core for troubleshooting those issues through the multiple sensors installed to search in detail what happens in the factory 24/7. These sensors form the foundation of any troubleshooting system by capturing essential data, but the real value lies in creating an effective strategy that integrates IoT platforms, Edge Computing, Machine Vision, AI, AR, mobile apps, and other components in a unified solution.
Real-time Monitoring and Alerting
IoT sensors installed on equipment or in operational premises track the system's health every second delivering continuous data flow to the central hub. Such precise, real-time monitoring allows for immediately detecting abnormalities and rapid response. When a machine starts to underperform, sensors capture temperature spikes, excessive vibration, energy consumption surges, and other essential metrics to identify deviations and send alerts to maintenance teams. These alerts enable quick reaction, preventing small issues from turning to production downtimes with hundreds of thousands of dollars in expenses.
For example, in the automotive sector, IoT sensors embedded in production lines can detect irregularities during engine assembly processes by measuring vibration levels and torque. Any deviation from the standard triggers an alert, allowing technicians to address the issue before it leads to a critical failure. IoT also serves as a cornerstone for advanced quality control processes often handled by collaborative robots.
Root Cause Analysis and Fault Isolation
Identifying the root cause of a problem can be challenging when an issue occurs suddenly. IoT provides greater transparency to all the processes at each step of production helping to instantaneously track down the source of the fault. This targeted troubleshooting capability allows production staff to isolate issues quickly, rather than relying on time-consuming trial-and-error methods. For instance, in highly complex and sensitive semiconductor manufacturing, IoT can track all the stages of the wafer production process to detect the reason for the defect, be it machine miscalibration or environmental fluctuation.
The more data applied to analysis, the better the identification of larger-scale issues. For example, a recurring miscalibration can indicate problems with either a vendor or maintenance procedures. Addressing the issue strategically can substantially reduce costs by preventing failures, downtime, and defective batches.
Remote Diagnostics
IoT in manufacturing enables remote diagnostics by giving engineers access to machine data from anywhere in the world. This capability is especially valuable for manufacturers with widely distributed facilities. IoT can also be combined with AR glasses to provide remote engineers' expert instructions, improving maintenance accuracy. Troubleshooting can be significantly accelerated without the need for physical presence.
For instance, wind turbine operators use IoT sensors to monitor turbine gearbox performance. When a fault is detected, the issue can be diagnosed remotely, allowing engineers to recommend maintenance actions before an on-site visit is necessary.
Need Assistance with IoT in Manufacturing?
Digital Twins for Virtual Troubleshooting
A digital twin replicates a physical object, system, or process by using inputs from IoT sensors to simulate various "what if" scenarios. This enables digital twins to test new technological approaches in production and identify potential bottlenecks before they arise.
Digital twins can be accurately created for machines, systems, production lines, shop floors, or entire factories to evaluate multiple troubleshooting methods while keeping manufacturing operations running smoothly. This "virtual troubleshooting" approach provides a highly efficient way to determine the best procedures for resolving issues.
For example, digital twins demonstrate significant value in critical applications, such as aircraft engines. In real-time, they collect both operational and historical data to simulate different performance scenarios and predict potential faults. This predictive capability enables the creation of maintenance schedules that are optimized to prevent problems before they arise, significantly reducing the likelihood of expensive failures during critical operations like flights.
The Role of Machine Learning: Anomaly Detection & Predictive Maintenance
When IoT in manufacturing incorporates Machine Learning (ML), it enables true intelligent production. ML algorithms process vast data streams to identify abnormalities that may not be detectable through human inspection. Once an anomaly is detected, IoT systems can automatically initiate troubleshooting protocols, such as adjusting machine settings, alerting maintenance teams, or shutting down equipment to prevent hazardous situations. For applications requiring instantaneous responses, mastering Edge AI is crucial to enable comprehensive processing within a device without relying on cloud computing.
As a result, issues such as leaks, blockages, pump failures, misalignment, imbalance, bearing wear, cooling system failures, insufficient lubrication, electrical faults, and other inefficiencies can be addressed through IoT-based predictive maintenance. Additionally, IoT-enabled machine vision systems are increasingly used to enhance inspections by processing real-time video streams to detect defects. These machine-learning algorithms are trained on vast amounts of data to ensure fault identification with the highest precision.
Beyond manufacturing, IoT-based anomaly detection is increasingly adopted in healthcare to diagnose diseases based on medical data such as CT scans, medical history, and real-time monitoring of vital signs and other critical parameters. Moreover, it is a key technology for autonomous vehicles, which must reliably detect anomalies on the road.
IoT in Manufacturing: Troubleshooting Benefits
To develop an effective advanced troubleshooting strategy, focus on turning the main benefits into targeted goals. With IoT in manufacturing, you can achieve the following outcomes:
By automating real-time issue identification, resolving problems quickly, and adopting predictive maintenance practices, factories can significantly reduce emergency repair costs and prevent expensive unplanned downtime.
Precise IoT-based monitoring ensures that no product batch contains defective items. Maintaining rigorous industry standards minimizes customer complaints and increases trust in your products.
Reducing faults naturally leads to smoother production with streamlined operations, end-to-end transparency, and increased manageability.
IoT generates large amounts of data that can be organized into reports for strategic enhancements. These improvements may involve processes, schedules, vendor management, workforce optimization, and more. As datasets grow, they facilitate continuous improvements to the production environment and help identify the best troubleshooting practices.
Overcoming Challenges of IoT in Manufacturing
As IoT adoption in manufacturing grows, more companies report positive implementation outcomes. These successes are often due to a strategic approach to risk management, addressing challenges that may arise during and after IoT deployment.
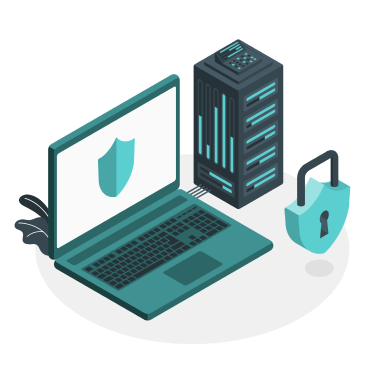
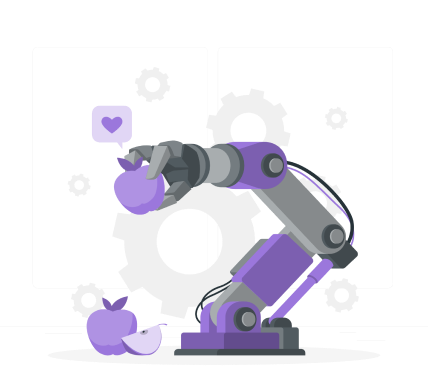
Challenges emerge when integrating diverse machines, sensors, and platforms from various vendors, as they may not always be compatible. Adopting standardized protocols and open APIs can help achieve seamless integration across different systems.
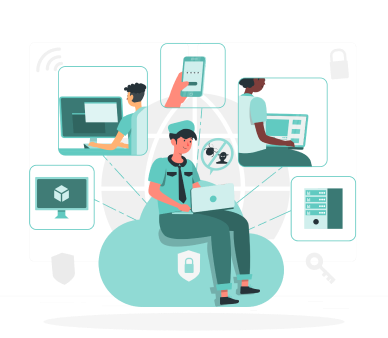
As manufacturing operations grow, IoT systems must evolve to handle the increasing number of connected devices and the expanding volume of data. To meet these demands, manufacturers should prioritize flexible IoT solutions that can expand and adapt to changing operational requirements. Investing in adaptable infrastructure ensures that the system remains efficient and responsive as technology advances and data needs increase.
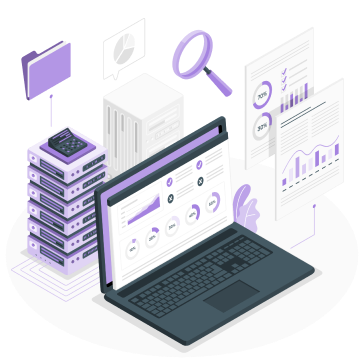
The sheer volume of data generated by IoT can quickly become overwhelming without proper strategies in place. Utilizing edge computing and advanced analytics helps manage data processing by filtering and analyzing information closer to the source. This approach reduces the load on centralized systems, facilitates real-time insights, and supports timely response for more efficient use of the data gathered.
Conclusions: Combating Unplanned Downtime with IoT in Manufacturing
IoT is reshaping how troubleshooting and maintenance are approached in manufacturing by shifting the focus from reacting to problems after they occur to preventing them before they arise. With tools like predictive maintenance and real-time monitoring, IoT in manufacturing enables to maintain peak efficiency and minimize unexpected downtime. This proactive approach allows for early detection of potential issues, enabling timely interventions that keep production lines running smoothly. As a result, manufacturers can streamline workflows, make informed decisions based on comprehensive data analysis, and drive continuous improvement in operational processes.
Looking forward, IoT's role in manufacturing appears limitless, offering a pathway to smart factories where interconnected systems and automation are standard. Although obstacles like data security and system integration persist, the advantages—such as improved productivity and problem prevention—clearly outweigh the challenges. This progressive approach is paving the way for a new era of industrial innovation and productivity, setting a foundation for a smarter, more resilient manufacturing landscape.