Blood Culture System: Simulation & Upgrading
Highlights
One of the world’s largest manufacturers of medical diagnostic instruments and reagents set out to expand its product line of blood culture systems – intuitive instruments for detecting bacteria in blood. They were preparing to launch a compact version to fit smaller laboratories, and planning further extensions for the original system, which had proven to be quite cost-intensive. Partnering closely with the client’s diagnostics department, PSA stepped in to support the development efforts.
Challenge
Client Challenge
Optimize product lifecycle costs of the blood culture system, considering its development, maintenance, and the launch of new product variations.
Project Objective
Provide simulation and cost-effective modernization for the current blood culture system, while also finalizing the development of the updated version.
Solution
To provide greater flexibility in developing both existing and new products, the PSA team enabled its simulation by providing precise desktop control. For this, we ported the blood culture system software from embedded (VxWorks) to Windows OS, allowing it to connect to the existing hardware simulator. Our engineering team carried out:
-
Business logic modifications to accommodate OS differences
-
Porting of the Zinc-based interface to support various screen sizes
-
Ensuring the simulation of printing, barcoding, communication ports, reports, and dynamic screen sizing functionality
By validating on the simulator first, PSA enriched the blood culture system with multi-language support, safe reboot, an on-screen keyboard and debug console, and improved alert and barcoding functionality.
To bring the compact blood culture system to market and facilitate its further development, the PSA engineering team made key modifications to two original systems:
-
The instrument app to support operations with half of the number of blood vials
-
The simulator to match the new product hardware
We updated the source code and interface screens to reflect these capacity changes, while also adding mobile connectivity for smartphone control.
During an onsite trip, we assisted the client with safe and thorough feature implementation, testing, and bug fixing, ensuring the reduced blood culture system was ready for a swift market launch.
As a result, our client gained a precise testing and validation environment for both products while the new product was fully prepared for its market debut
Development Included
- Requirements Clarification
- Proof of Concept
- Software Porting
- Features & Drivers Implementation
- Testing & Bug Fixing
Results
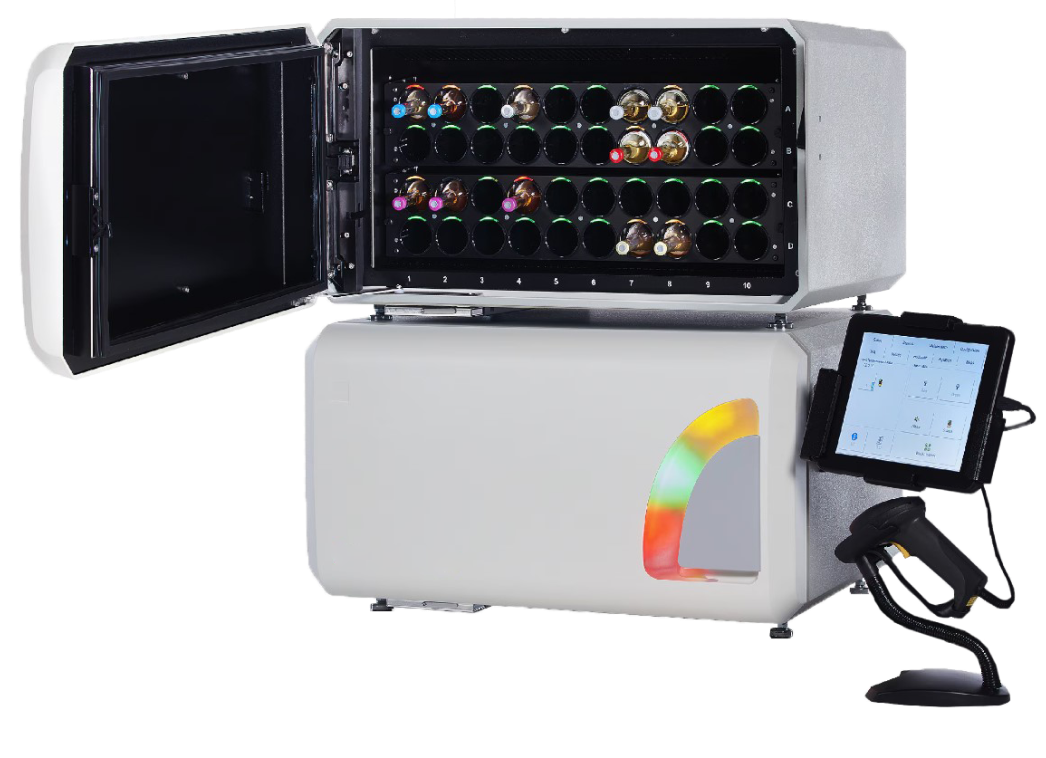
-
Simulation apps for both products completed
-
Original product modernized
-
The new product is market-ready
-
Development time and efforts reduced
Technology Breakdown
- 4 Software Engineers
- 16 months