Production Simulation System for Automotive Giants
Highlights
From 2017 through 2018, PSA was engaged in developing a production simulation environment to be used for hiring purposes by leading global automotive manufacturers. The highly customizable solution streamlines high-volume recruiting processes, which enables rapid, complete, and efficient assessment of whether a candidate complies with the production role requirements. Having deployed one at the customer’s site, our client requested substantial advancements so that it could be deployed for their other customers afterward.
Challenge
Client Challenge
Refine the production simulation system in terms of performance, flexibility, and customization to amplify its market value.
Project Objective
Redesign the production simulation system to provide consistent uptime, easy reconfiguration, and simplification of onsite deployment.
Solution
Based on the existing but troubled system, the PSA team designed a complete architecture for the integrated production simulation system. The core of this system can be universally implemented for multiple automotive giants. Primarily, we held onsite sessions for deep-dive system research, stakeholder interviews on business and technical expectations, and environmental analysis to engineer functional and non-functional requirements.
The proposed system comprises multiple testing stations simulating a real production environment to assess how a candidate performs work tasks. Modular and interconnected, the designed system involves the following components:
-
Core server module for data collection and participant testing
-
Several simulation station types to meet the needs of assessment centers
-
Inspection station for participant flow and simulation stations management
-
Sensor agents for simulation stations
-
Exams presented with correspondent equipment and connected sensors
-
Brand-customizable web and PC UI
The system is provided with the ability to introduce new station types and substitute modules created by a 3rd party through defined interfaces between modules and external systems. We ensured 24/7 remote access via the web browser using a secure connection protocol to enable handy administrator management.
We’ve ensured the system fully satisfies the client’s request by implementing the following functionality:
-
Input and import list of candidates and employees
-
Configuration of assessment exercises
-
Configuration of the assessment station
-
Performed simulation process operations on stations & process control
-
Scored the results and generate summaries with recommendations
-
Transferred test results data to the external HR system
-
Created local backups for test results
The PSA engineering team defined the system option for the primary customer, which required minimal modification of the existing equipment for cost savings. Also, we developed a PoC desktop app for one simulation station with custom peripherals attached.
Finally, PSA delivered a system architecture document defining requirements for stations, web portal, and administration module, as well as hardware constraints. This included use cases, components descriptions with diagrams showing modules and logical connections, sequence diagrams, interface definitions covering external and internal system interfaces, database schema definition, and deployment diagrams.
Development Included
- System investigation
- Onsite requirements definition
- Architecture design
- Software design
Results
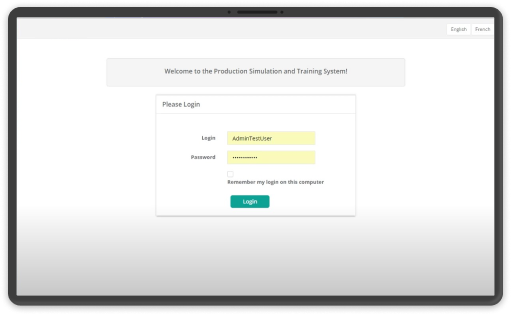
-
A refined system meets the urgent production needs
-
High-efficiency system concept can be proposed to end customers
Technology Breakdown
- 1 System Architect
- 2 Software Engineers
- 1 Technical Writer
- 7 months